ince 2013, Scala Filtration has been delivering quality compressed air purification equipment and laboratory liquid nitrogen generators around the world.
To lean more about latest technology and solution to compressed air treatment and liquid nitrogen generation,please contact us immediately.
Compressed Air Treatment & Liquid Nitrogen Generator
CL Series carbon steel coalescing filter
CL Series carbon steel coalescing filter
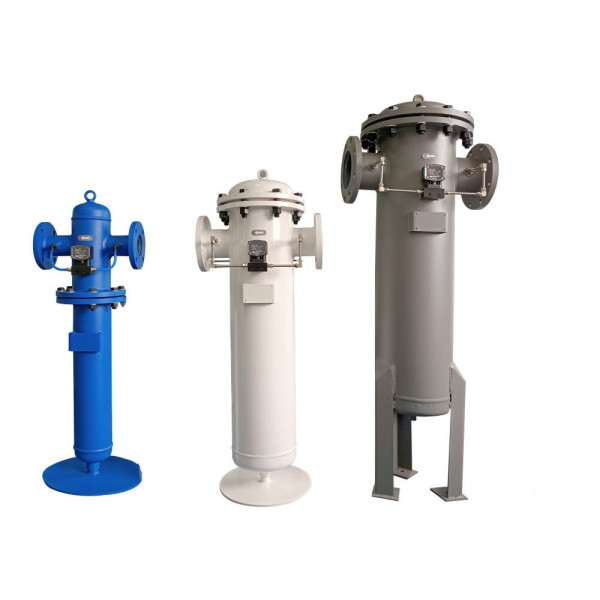
Categories | Thread Coalescing Filter |
---|---|
Brand | SCALA |
Model | CL180 |
Flow Rate | 18m3/min |
Max Pressure | 16bar |
Connection | DN65 |
Housing material | aluminum alloy |
Filtration Grade P | 3 micro |
Element replace period | 12months |
Optional | Inner Automatic Drain |
Accessories | Differential Pressure Gauge |
Unit Price | US $ 35 / piece |
FOB port | Shanghai |
Terms of Payment | T/T, Western Union |
Update Time | Apr 25,2025 |
CL Series carbon steel coalescing filter
CL Series carbon steel coalescing filter for users to provide high quality compressed air filter, special 1000 laser cutting blowing bottle, high grade spraying, food, electronics, petrochemical and other industries.
Features and Benefits
Carbon steel housing with special anti-corrosion treatment to improve durability and long lifetime.
The top of filter element is designed with a bayonet to save installation space and facilitate disassembly.
100% leak detection test to eliminate air leakage.
CL Series carbon steel coalescing filter filtration performance meets IS08573-12010 1(E) International Standard.
Equipped with pressure differential guage which can measure and display the pressure difference of filter element.
Dismountable float automatic drain with testing function,optional electrical level controlled drain.
Filtration Grade
Grade C: particulate: 3µm, oil content :3 ppm
Grade T : particulate: 1µm, oil content 1 ppm
Grade A: particulate:: 0.01lµm, oil content :0.01 ppm
Grade X particulate: 0.01µm, oil content: 0.003ppm(activated carbon)
Grade H particulate: 0.01µm, , Oil content: 0.001ppm
Grade F dust removal with 0.1µm precision
Grade FF super high efficiency dust removal, precision 0.01µm
Technical Specifications
Filter Model | Flow Capacity | Inlet/Outlet Connection | Element Model | Eement Quantity | Dimensions(mm) | Weight | ||
m3/min | cfm | A | B | Kg | ||||
CL180* | 18 | 635 | DN65 | E180* | 1 | 353 | 950 | |
CL220* | 22 | 776 | DN80 | E220* | 1 | 353 | 1110 | |
CL360* | 36 | 1270 | DN100 | FE180* | 2 | 465 | 1120 | |
CL450* | 44 | 1553 | DN100 | FE220* | 2 | 465 | 1270 | |
CL550* | 54 | 1906 | DN125 | FE180* | 3 | 500 | 1166 | |
CL660* | 66 | 2329 | DN125 | FE220* | 3 | 500 | 1285 | |
CL900* | 88 | 3106 | DN125 | FE220* | 4 | 565 | 1400 | |
CL1100* | 110 | 3883 | DN150 | FE220* | 5 | 617 | 1430 | |
CL1300* | 132 | 4659 | DN150 | FE220* | 6 | 726 | 1540 | |
CL1500* | 154 | 5436 | DN200 | FE220* | 7 | 726 | 1540 | |
CL1800* | 176 | 6354 | DN200 | FE220* | 8 | 780 | 1580 | |
CL2000* | 198 | 6989 | DN200 | FE220* | 9 | 800 | 1580 | |
CL2200* | 225 | 7942 | DN200 | FE220* | 10 | 800 | 1585 | |
CL2600* | 264 | 9219 | DN250 | FE220* | 12 | 860 | 1570 | |
CL3000* | 308 | 10872 | DN250 | FE220* | 14 | 860 | 1590 |
The coalescing filter is mainly designed for liquid-liquid separation. It contains two kinds of filter elements, namely: poly filter element and separation filter element. For example, in the oil dewatering system, after the oil flows into the coalescing separator, it first flows through the coalescing filter element. The coalescing filter element removes solid impurities and coalesces tiny water droplets into larger water beads. Most of the coalesced water beads can be separated and removed from the oil by their own weight and settled into the sump. Then the oil flows through the separation filter again. Because the separation filter has good lipophilicity and water repellency, the water is further separated. Finally, the clean, anhydrous oil flows out of the coalescence separator.
The oil first enters the lower part of the filter housing through the inlet pipe, and then flows into the filter core from the outside, then the coarse particles will immediately settle down and be discharged by the sewage valve. The smaller particles are intercepted by the filter core. Finally, the clean oil is collected by the filter element tray, and then flows out of the coalescing separator through the outlet pipe. As the amount of oil being processed increases, the contaminants deposited on the filter element will cause the pressure difference of the coalescer to rise. When the pressure difference rises to 0.15Mpa, it indicates that the coalescing filter element has been blocked and should be replaced.
The oil flows from the oil inlet of the coalescing separator into the first-level tray, and then shunts into the first-level filter element. After filtration, demulsification, water molecule growth, and coalescence, impurities are trapped in the first-level filter element, and the coalesced The water beads settle in the sedimentation tank, and the oil enters the secondary filter element from outside to inside, collects in the secondary tray, and flows out from the outlet of the coalescence separator. The material of the secondary filter element is hydrophobic, the oil can pass through smoothly, and the free water is blocked outside the filter element, flows into the sedimentation tank, and is discharged through the dirt release valve.
- Loading...
- Tel
- *Title
- *Content
- laboratory liquid nitrogen generator delivered to Tibet College of Agriculture and Animal HusbandryRecently, our company successfully supplied a self-developed laboratory liquid nitrogen generator for the Plant College of Tibet University of Agriculture and Animal Husbandry, with a liquid nitrogen output of > 20 liters per day.
- Hangzhou Scala officially launched silent laboratory liquid nitrogen generatorAs a professional laboratory liquid nitrogen solution provider, Hangzhou Scala recently officially launched a new integrated liquid nitrogen generator, the equipment is small, low noise, high degree of automation, easy to use and maintain. After more than a year of internal testing, all parameters have met the expected requirements.